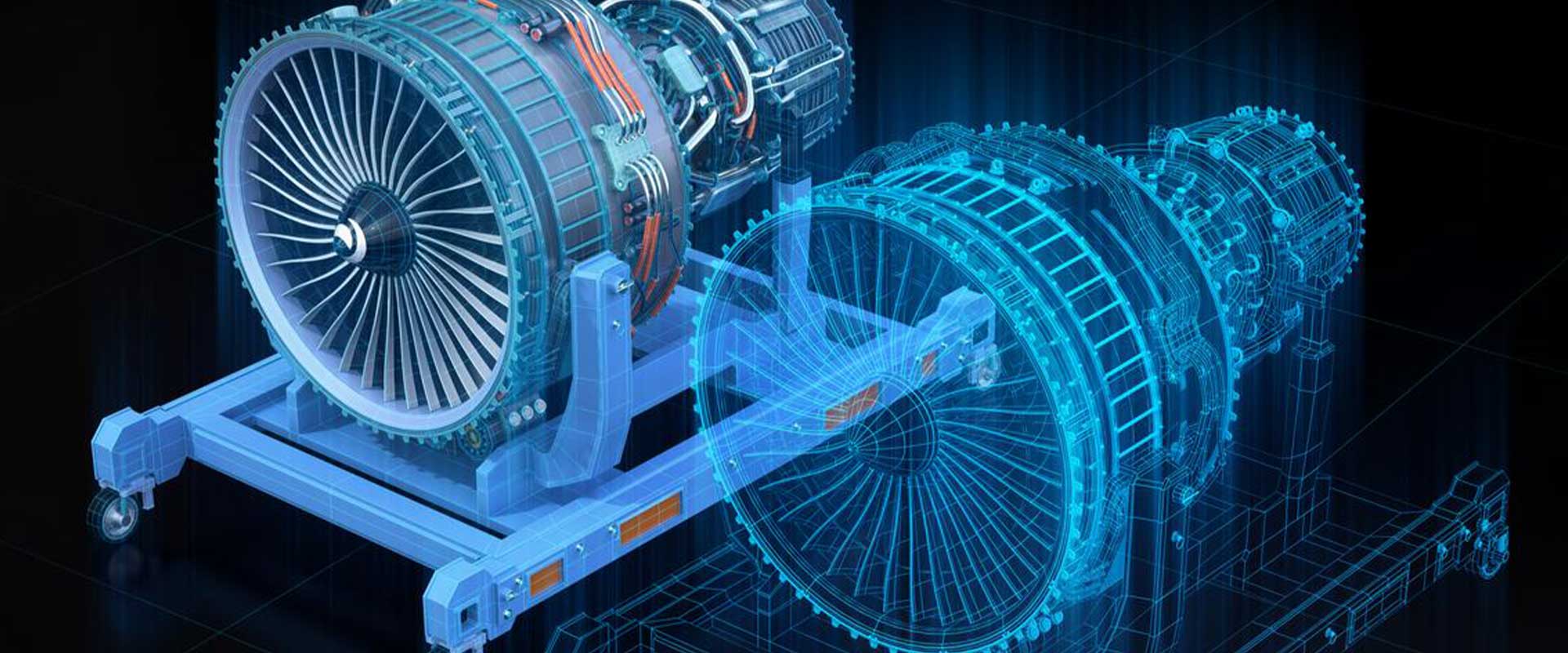
Industrial engineering has significantly evolved over the decades, largely driven by continuous digital advancements. The foundation of such advances was laid by digitalization that was accelerated by the digitalization of information, integration, and utilization of digital tools, automation, connectivity, and analytics to optimize efficiency, productivity, quality, and safety to improve industrial processes, systems, and decision-making.
Digitalization has had a profound effect on Original Equipment Manufacturers (OEMs). It has led to significant changes in how these companies design, manufacture, and distribute their products, as well as how they interact with their customers and suppliers. Historically, the introduction of Computer-Aided Design (CAD) and Computer-Aided Manufacturing (CAM) systems enabled engineers to design and model parts digitally, eliminating the need for physical prototypes. The 2000s saw the rise of the Internet, which opened up new avenues for collaboration and communication among design teams, suppliers, and customers.
In recent years, the fourth industrial revolution, or Industry 4.0, has brought new opportunities and challenges for OEMs. It involves the integration of digital technologies such as the Internet of Things (IoT), artificial intelligence (AI), big data analytics, and advanced robotics into the manufacturing process, allowing for even greater automation and efficiency.
Today, the Internet of Things (IoT), big data analytics, blockchain and AI, and other emerging technologies play a critical role in this digital evolution, contributing to the rise of “Digital Twins” and predictive maintenance.
Evolution and Implementation of Digital Twins
Digital Twins—dynamic, virtual replicas of physical systems—originated in the late 1960s when NASA began using mirrored systems to simulate conditions in space1. Over the years, as computational capacities expanded and IoT technologies matured, Digital Twins have become instrumental in modeling, monitoring, and optimizing business operations in real time.
The global Digital Twin market size was valued at USD 3.1 billion in 2020 and is projected to reach USD 48.2 billion by 2026. Various industry leaders have employed Digital Twins to optimize operations.
Drivers and Hurdles of Digitalisation
The shift towards digitalization and the creation of Digital Twins has several catalysts, including the rise of IoT, the need for efficient product design and production, and the growing demand for predictive maintenance. Furthermore, sustainability trends and the adoption of Industry 4.0 principles significantly contribute to this movement.
However, few notable hurdles exist. These include the absence of standardized data formats and protocols, cybersecurity threats, and significant initial investment in IT infrastructure and software. Additionally, managing the massive data generated by Digital Twins requires advanced data analytics capabilities.
Servitization and New Revenue Models
The rise of predictive maintenance has given way to servitisation, where OEMs shift from selling products to providing comprehensive solutions. Servitisation has been transforming product-centric business models into one that combines products with value-added services. Here’s how OEMs are leveraging servitisation to achieve these objectives:
- Pay-per-Use Models: Instead of customers purchasing equipment, they pay based on actual usage, which allows for greater flexibility and scalability.
- Product Lifecycle Management: This includes installation, maintenance, repairs, upgrades, and disposal/recycling services. By providing end-to-end support, OEMs ensure the optimal performance and longevity of their products, which helps reduce costs and downtime for customers.
- Performance-based Contracts: Manufacturers supplying industrial equipment can charge based on the level of productivity, uptime, or energy efficiency delivered by the equipment. This incentivizes both the OEM and the customer to work collaboratively to achieve the desired results.
- Data-driven Services: By collecting and analyzing data from connected products, manufacturers can provide insights, predictive maintenance, and optimization recommendations to customers. These data-driven services help improve efficiency, reduce downtime, and enhance overall performance, creating additional revenue streams for the OEMs.
- Asset Financing and Leasing: Rather than purchasing equipment outright, OEMs’ customers are increasingly exploring leasing or financing industrial equipment, paying regular installments over a defined period. This allows customers to conserve capital, access the latest technologies, and easily upgrade or expand their equipment as needed.
This transition paves the path for new revenue models. Rolls-Royce’s “Power-by-the-Hour” is a noteworthy example of this trend, where customers pay for engine usage instead of owning the engines.
Digital Twins and predictive maintenance strategies allow companies to transition from capital expenditure (CAPEX) to operational expenditure (OPEX) models. Companies can avoid substantial upfront costs by paying for services or usage instead, leading to more predictable and manageable OPEX.
Quest Global: Transforming Maintenance with Digital Twins
As a global leader in engineering and digitalization, Quest Global has played a crucial role in driving the adoption of Digital Twins and predictive maintenance4. By integrating IoT, AI, and machine learning, we have transformed clients’ business models across various sectors.
In conclusion, although the digitalization journey and the creation of Digital Twins are fraught with challenges, they hold immense potential for businesses. With leaders like Quest Global at the helm, companies can successfully navigate this transformative landscape.